Outbuild is online scheduling software to work together on connected project schedules and look-aheads, enabling everyone to move faster.
Key Takeaways
Table of contents
- What is Construction Sequencing?
- Importance of a Well-Planned Construction Sequence
- Key Elements to Consider in Building Construction Sequence
- Creating a Timeline for Efficient Construction Sequencing
- The Role of Technology in Optimizing Construction Sequences
- Common Mistakes to Avoid in Construction Sequencing
- Conclusion
What do you do when you need to renovate an occupied hospital building?
There are a few options. You can vacate the building for months or years while you get the work done. This can make the project go faster, but it has some major drawbacks. During that time, patients may have to travel much farther to another hospital, putting them at risk. The financial impact on the hospital is also enormous, with thousands of patients seeking medical care elsewhere.
But, there is another option – construction sequencing.
Construction sequencing is a method of construction planning that allows building sites to remain in operation even while renovations are ongoing. Splitting the work into phases and only shutting down areas that are currently under construction allows sites to remain mostly open. The real benefit of this method is in locations where shutting down entirely is either impossible or prohibitively expensive. Some construction sequence examples include roadways, hospitals, police stations, and sites where environmental impact is a concern. Pulling off a project like this is no easy task. With dozens of subcontractors and hundreds of workers, there are a lot of moving parts.
Managing a large-scale construction project is complicated at the best of times, and keeping the site operational and minimizing environmental impact makes it even harder. Putting together a construction sequence plan is integral to keeping your project on track and has many benefits, including cost savings, better quality assurance, improved safety, and timely completion.
In an industry where 72% of firms say projects have taken longer than anticipated and 78% of engineering and construction companies believe that project risks are increasing, it’s easy to see why starting with a top-notch building construction sequence is important.
Often, the elements that need the most consideration are unique to the project you are working on. For instance, if you are trying to minimize erosion on a site near a river, reinforcing stream beds, clearing, and grading should be at the top of your list.
But, there are still a few elements that are applicable in most situations. Consider these factors and questions before starting a project:
- Project scope and deliverables - What does the end product look like at the end of each phase?
- Phase space availability - Is your crew working on a few rooms, a floor, or a whole building in each phase?
- Resources - Do you have the labor, equipment, and materials needed for each phase?
- Lead times - How much in advance do you need to have crews, materials, and equipment scheduled to ensure they are there at the right time?
- Safety - Are you rushing your crews through a phase in a way that might promote cutting corners on safety?
- Phase transitions - Do you have a clear transition process communicated with the client of how they will move out and back in as the project progresses?
To explain this process, let's take a look back at that hospital.
We need a timeline that will keep everything on schedule while leaving key elements in operation. We can’t cut the power or water off to areas filled with patients. We can’t block the ER entrance with a parked cement mixer. We must ensure doctors and patients can get where they need to without walking through an active construction site.
So how do we do all this? By using four key steps to prepare for creating a timeline that works:
- Pre-construction planning: In sequence construction, it’s essential to know every possible project detail before you get on site. Factors like hospital operational plans, infection control protocols, and needed permits and inspections impact all the other steps in the process.
- Create a work breakdown structure: In this step, break down the project into phases while prioritizing critical areas. For example, moving the ER to another section of the hospital while it is an active phase.
- Sequencing based on dependencies: Now that you have the phases settled, you must ensure that they are not interrupting either each other or the function of the hospital. Ensuring noisy demolition happens during off-peak hours, verifying that pipes are in place before fixture installation, and making sure crews are not working near infectious diseases all fall into this step.
- Estimating durations and lead times: The final step before building the timeline is ensuring the length of each phase is realistic. This involves talking to subcontractors and noting hospital operational hours to find out how long your crews can work each day. You also have to consider how long it may take you to get needed materials or experts on site. If you are only able to work in the cancer center for a week in August, you’d better be sure all the materials are ready to go before that time.
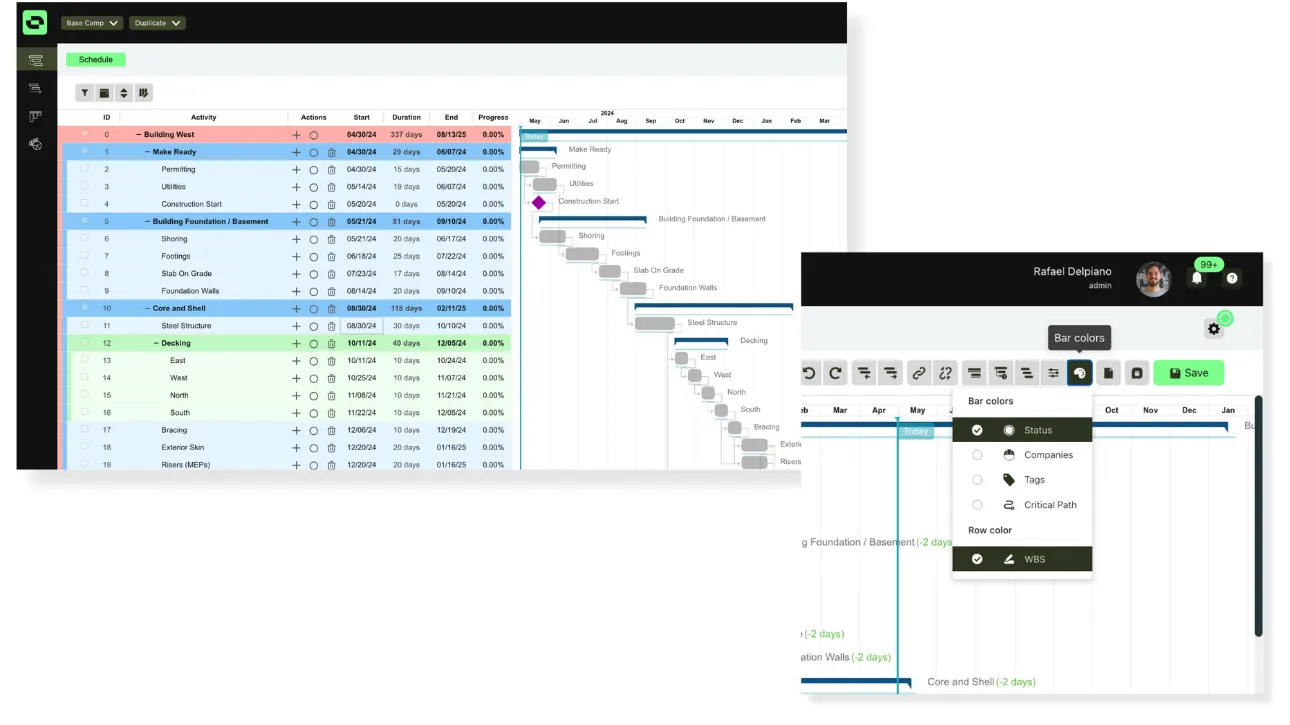
Finally, you are ready to build your timeline. Keeping all of this organized is not easy, which is why you need advanced collaborative scheduling tools like Outbuild, which allows unlimited users with different levels of permissions, are incredibly useful to ensure that everyone is aware and aligns with the plan, empowering other participants to be part of the process and to stay on top of it. Live and breathing Gantt charts can be a lifesaver here, along with agile software that can help you organize the project and adapt to the inevitable snags you are going to run into.
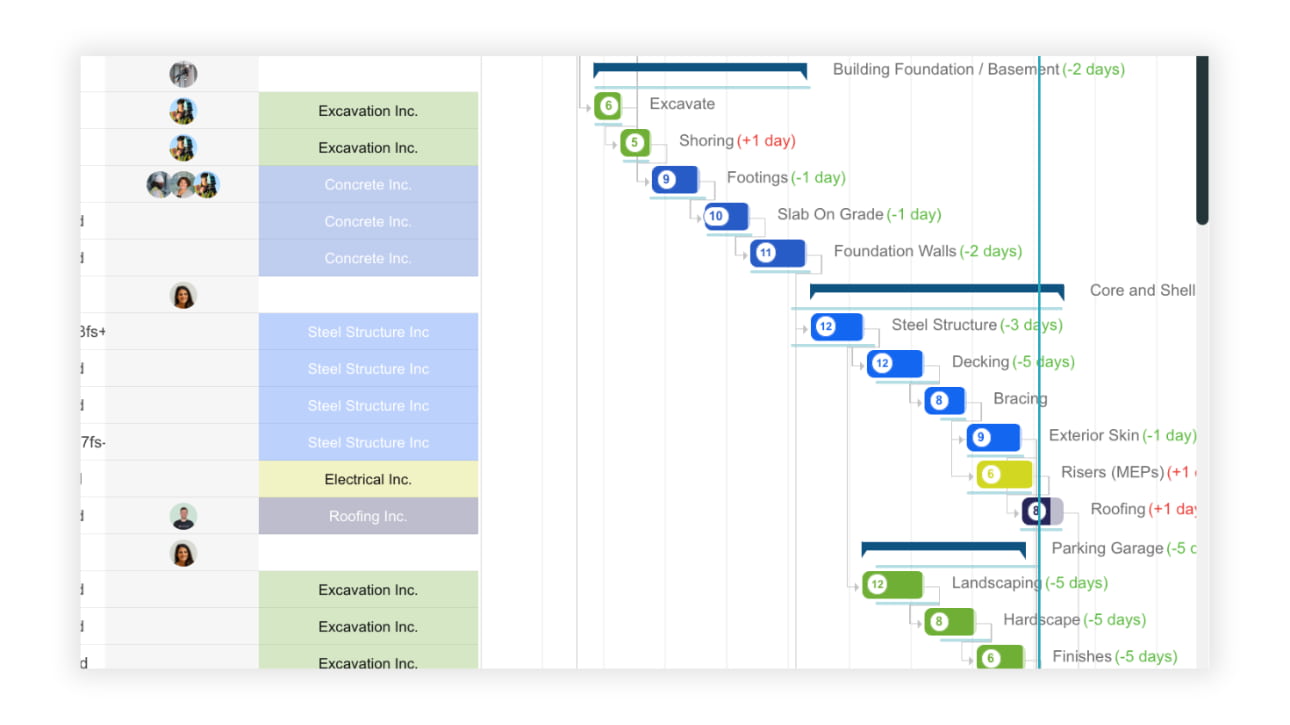
Thankfully, we’ve moved past the days of organizing the sequence of work in building construction with a clipboard and pencil. Huge advancements in management software have reshaped every aspect of the process.
Building Information Modeling (or BIM) is a technology that creates a digital 3D model of the entire building project from start to finish so clients can see what every phase will look like before you start. Digital twin technology takes this concept and applies real-time data so that the simulated version not only reflects the plan, but on-site conditions as well. Project management software offers basic tools for scheduling, while dedicated construction scheduling and planning software like Outbuild allows factors in resource availability, spatial constraints, “what-if scenarios”, integration with Procore, one-click Lookahead plans, and other key aspects unique to scheduling.
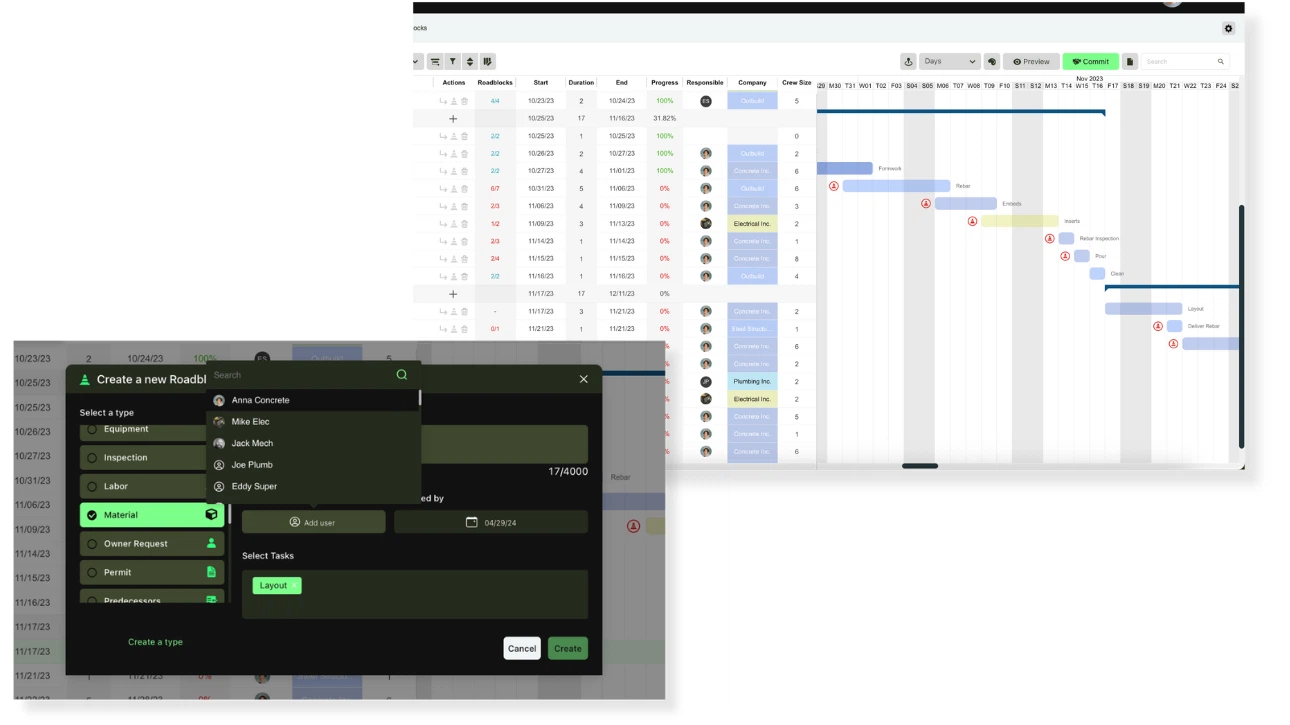
Getting the sequence of work in building construction right involves dozens of moving parts, making the entire process incredibly complicated. There are a lot of places where things can fall apart. But, with the right knowledge and tools you can bypass these common mistakes.
Missing or Ignoring Dependencies
Maybe one of the most common and most damaging to a project. A crew that gets on site and discovers they can’t get to work because they have to wait on some other prerequisite can send your project schedule toppling like a row of dominos.
Inflexible Scheduling
Lead times are hard to pin down - you get promised materials will arrive on the 10th and they show up on the 21st. You need to communicate with your clients and crews that you are building in wiggle room where you can. Determine what tasks can be done while you are waiting for materials, permits, and other delays.
Not Using Technology
Trying to manage the thousands of factors in a large-scale project using a notebook and Post-it notes just doesn’t work. You need to lean into the available tools as much as possible. Cutting corners here could cost you big time in the future.
Ignoring Limited Resources
After you have a draft of your schedule but before you start, you have to make sure workers, building supplies, and needed equipment are available for the start of each project phase. Missing even one of these could set off a chain reaction that could wreck your construction sequence of work.
Construction sequencing takes the complicated process of project management and cranks it into overdrive. But, when done right, it makes it possible to save time, money, and minimize negative impacts on communities. The key is having the tools built specifically with sequencing factors in mind. Outbuild Software includes the granular-level management tools essential for a successful construction sequencing project.
Related Articles
Ready to see Outbuild?
Join hundreds of contractors from 10+ countries that are saving money by scheduling better