Outbuild is online scheduling software to work together on connected project schedules and look-aheads, enabling everyone to move faster.
Key Takeaways
You know the pain of it. Showing up to the construction site with expectations for how the day has been planned, only to take a figurative punch to the gut when you notice that completed work will require rework.
Rework in construction remains one of the largest areas today that builders can improve efficiency and project profitability.
By leveraging the best tools for construction project management, scheduling and planning, large amounts of construction rework can be avoided by general contractors and trade contractors.
This article will help define what construction rework is, the cost of construction rework and how to reduce rework in construction.
Table of Contents
- What is construction rework?
- What does construction rework cost on an average project?
- What are the 5 most common causes for construction rework?
- How can field planning help avoid construction rework?
- Use the best scheduling and planning software to beat the construction industry average
- Other strategies to avoid construction rework
Construction rework is the process of correcting mistakes that have been made in the course of a construction project.
The cost of rework can be substantial and has long-term impacts on both time and budget. Unfortunately, construction rework is a common issue in the building industry. According to studies, up to 25% of all construction projects are delayed or over budget due to errors and omissions that require corrective action, which can be extremely costly.
Because of this construction schedules must be updated at least every 4 weeks, often also requiring 2-week or longer schedule look-aheads to ensure information is getting to the right people. In saying this, a LOT can happen in 2 weeks and in fact, most could argue that the schedule being updated weekly or even daily would see considerable gains in communication and preventing delays.
Research shows that the cost of construction rework is approximately 5-10% of overall project costs. This can range from minor changes and adjustments to complete demolition and reconstruction. In addition to the direct costs associated with materials, labor, equipment rental, and disposal, there are also indirect costs associated with construction rework such as lost time, decreased productivity, and potential project delays.
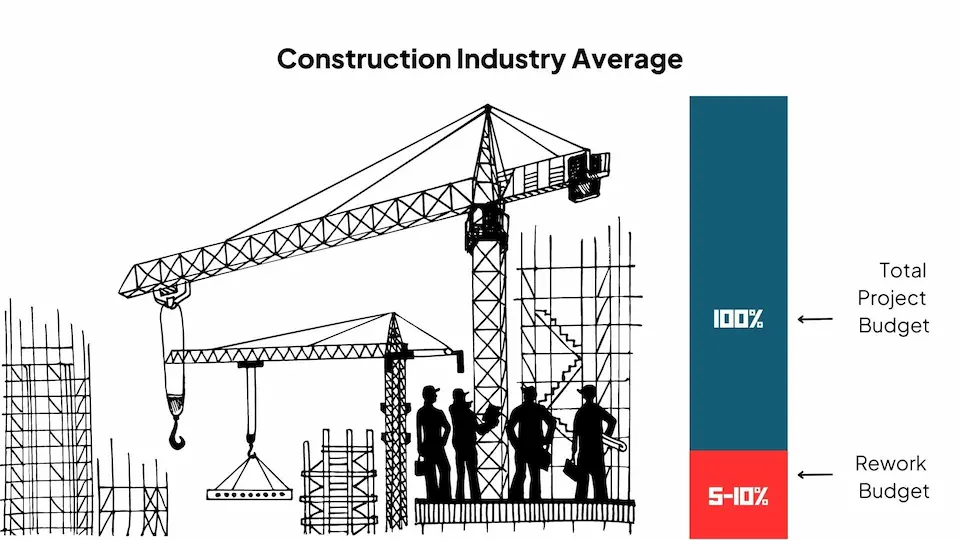
- Poor Planning – Taking shortcuts or not adequately planning for contingencies can cause problems down the line that require time-consuming rework.
- Poor Communication – Miscommunication between the contractor and owner/architect can lead to costly mistakes that require rework.
- Incorrect Installation – This is a common issue, as workers may incorrectly install items or components based on incorrect measurements, using bad materials or design errors.
- Lack of Quality Control – This is especially true for projects with multiple subcontractors, as quality control measures may not be in place to catch errors before they become expensive problems.
- Poor Material Selection – Selecting the wrong materials can lead to costly rework and project delays as the contractor is forced to order new materials to complete the job.
The best way to avoid rework is to have a comprehensive field planning process in place for your construction projects. Field planning should begin early and involve the entire project team so that everyone is on the same page as to what needs to be done and when.
This includes making sure all stakeholders are aware of any changes or updates that need to be made to the schedule or plans. Field planning should also include regular inspections, quality control measures, and open communication between all parties involved. By being proactive rather than reactive with field planning, many costly construction rework issues can be avoided altogether on a project.
Outbuild’s construction planning software is the first of its kind to connect your master schedule directly to your look-ahead so that adjustments made on the look-ahead can be shared in real-time to the schedule for approval. Often the cost of rework is simply tied to communication of field related information not getting to the scheduling team members fast enough and avoiding construction rework starts with improving communication at all levels.
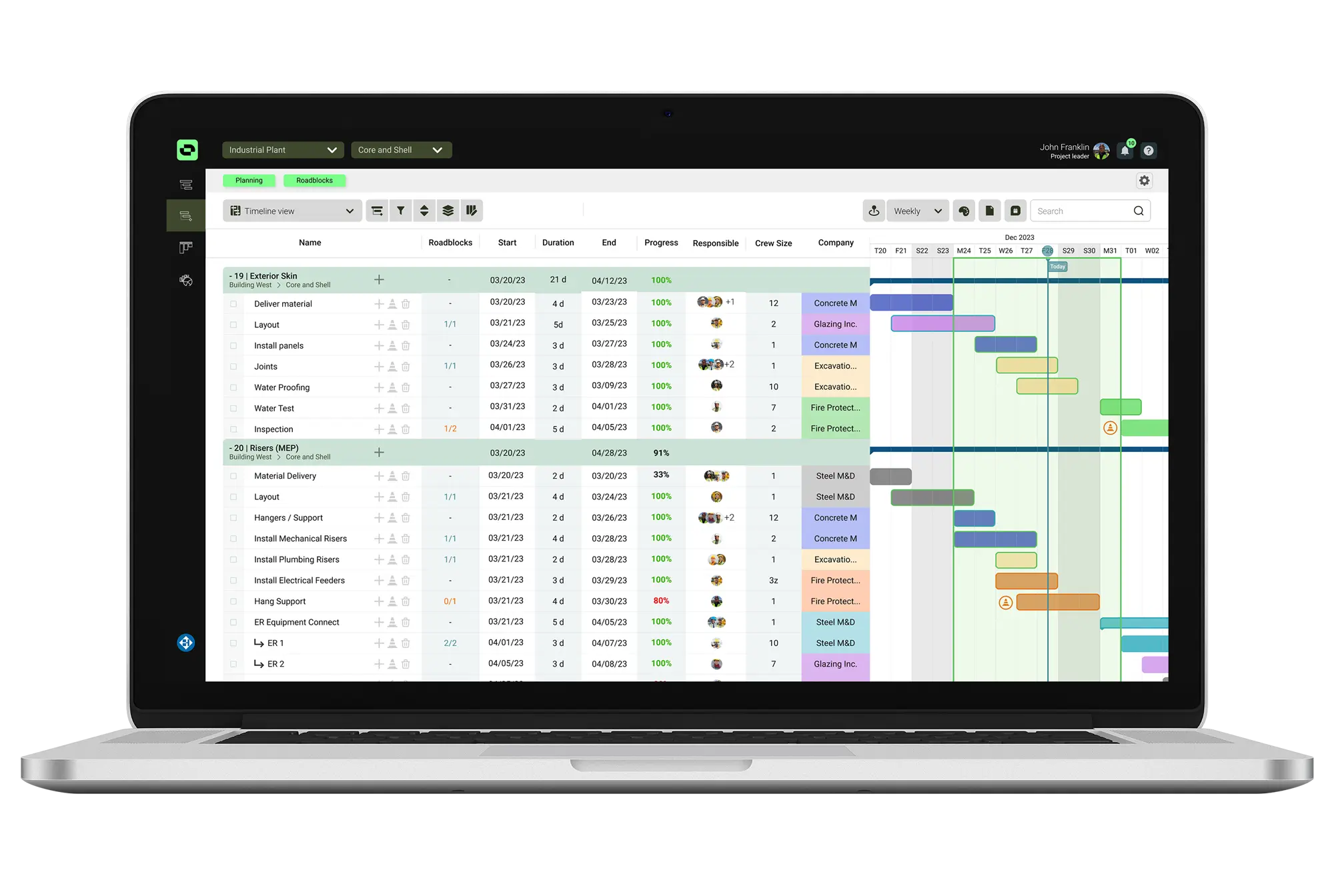
With Outbuild's connected scheduling and planning software, your field teams can create custom schedule look-aheads directly from your master schedule and instantly break down activities into smaller sub-tasks.
One of the best ways to implement new software in a company to avoid costly rework is by investing in project scheduling and planning tool that are designed specifically for the construction industry.
These tools can help streamline communication across all stakeholders, provide better visibility into the entire project timeline and even allow real-time adjustments when issues arise. In addition, these tools can be used to track costs, create and monitor project budgets, and identify potential areas for rework before they become a reality.
The key to avoiding construction rework is to be proactive in identifying and preventing errors before they negatively impact your job sites. This means establishing clear communication between the design team, contractors and subcontractors, as well as having comprehensive plans for quality standards.
It is also important to factor in time for rework during project planning, as it will take time away from other tasks. Having a rework budget that is separate from the main project budget can be helpful in preparing for any additional costs associated with the correction of mistakes.
Finally, it’s important to learn from mistakes and use them as an opportunity to make improvements in the future. By understanding what went wrong and how it could have been avoided, it’s possible to reduce the risk of similar errors in future projects.
In conclusion, we all experience some degree of construction rework on our projects but we also can likely all agree that we can get better in this area. Better planning and better communication are the top ways to reduce the cost of rework in construction companies and leveraging tools like Outbuild is a smart place to start.
Related Articles
Ready to see Outbuild?
Join hundreds of contractors from 10+ countries that are saving money by scheduling better